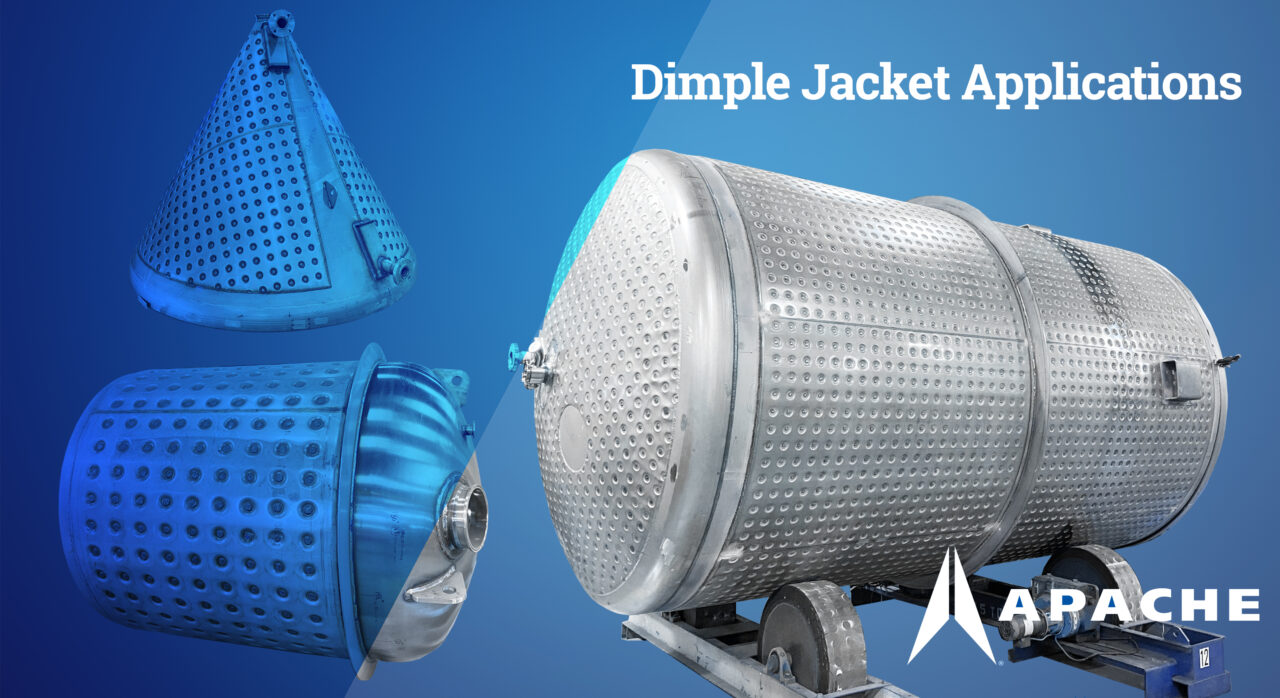
Thermal heat exchange surfaces control the temperature of pressure vessels and are engineered for the application and use of the vessel. While there are several methods used in engineering design of ASME vessels, the dimple jacket design supports flexibility and versatility required in some applications.
Dimple jackets utilize a thin gauge stainless steel layer that is plug welded to the vessel shell in a regular pattern. The punched and spot-welded areas are called dimples, which create turbulence of heat or cooling fluid flowing through the jacket. The dimple jacket design provides exceptional strength under uniform temperature and pressure loading.
Applications:
• Steam Heat and Cooling Transfer Media
• High jacket pressure up to 290 psig at 300° F.
• Large expansive areas of heating or cooling.
• Zoned jacketed areas to provide processing efficiency.
• Versatility is required for shape and size.
Steam & Cooling Applications: Dimple jackets are well suited to steam applications. The dimple jacket provides efficient heat transfer at low media flow. The dimple jacket surface is a safe design for uniform temperature controls. The dimple jacket can be used for cooling during other process steps, saving a separate thermal process stage which increases productivity and efficiency.
Jacket Pressure and ASME ratings: Dimple jackets are manufactured for several different pressures and patterns. Apache provides both 12 ga. and 14 ga. materials for dimple jacket construction. Each pattern is validated, and proof tested per ASME regulations. High jacket pressures are permitted without significant increase of side structure thickness. Every application is evaluated during the compliance design verification stage to make sure the proper jacket pressure and temperature rating is utilized before project and cost approval.
Large Heat Transfer Area: The dimple jacket is commonly used in large tank design. On large tanks, dimple jackets have a lower price point and maintain a higher-pressure drop compared to conventional jackets.
Zoned Jacketing: Jackets can be applied to the entire surface of a vessel or divided into zones to provide flow of heating or cooling medium. The benefit to having more zones is better efficiency in transferring heat while reducing pressure drop in the jacket. However, it does result in more inlets and outlets to manage, so that must be considered in overall design requirements.
Shape & Size Versatility: Dimple jackets can be utilized in all parts of a vessel on shells and heads where room allows. Dimple jacket shells can conform to all types of processing vessels sizes and shapes used in the chemical, food and beverage, biopharma, and health industries.
Applications that are subject to rapid thermal cycling are not recommended for dimple jacket solutions.
It is important to partner with an experienced and reputable partner for ASME engineering and manufacturing of heat transfer vessels. Apache Stainless has been ASME certified for over 40 years and is accredited with many other global standards.
For more information and Heat Transfer Surfaces, read our guide “Abstract and Attributes of Heat Transfer Surfaces”.